6m Fishbone Diagram Projects - Jika kamu mencari artikel 6m Fishbone Diagram Projects terlengkap, berarti kamu sudah berada di web yang tepat. Setiap artikel dibahas secara lengkap dengan penyajian bahasa yang gampang dipahami bagi orang awam sekalipun. itulah sebabnya situs ini banyak diminati para blogger dan pembaca online. Yuk langsung aja kita simak ulasan 6m Fishbone Diagram Projects berikut ini.
6m Fishbone Diagram Projects. This diagram looks like a fish skeleton. And its called a Fishbone Diagram because it looks a bit like a fishbone. The Cause and Effect diagram also known as Fishbone Diagram proves extremely beneficial when exploring or dissecting any production or industrial operations problems. The 6 Ps originated when more and more companies began migrating Lean to the office. Login to your account OR.
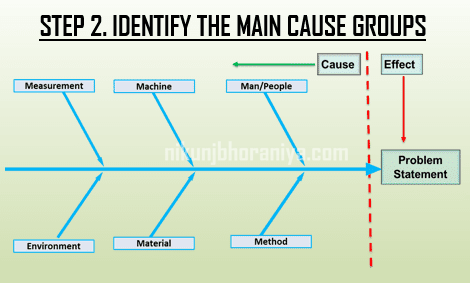
Food Loop Diagram Examples presented here will help you to understand the concept and you can also use the same template for your project. Fishbone diagram or Ishikawa diagram is a modern quality management tool that explains the cause and effect relationship for any quality issue that has arisen or that may arise. Fishbone is also known as cause and effect diagram or Ishikawa diagram. Once all inputs are established on the fishbone you can proceed with the 5 Whys technique to drill down to the root causes. A fishbone diagram is a tool that can help you perform a cause and effect analysis for a problem you are trying to solve. The Cause and Effect Diagram is also known as the Fishbone Diagram and the Ishikawa Diagram.
Advanced options are available to put the CE diagram to use for more complex problems.
Switch Wiring Diagram Pdf The head is the problem and the causes are connected with the spine. Each cause or reason for imperfection is a. It is a problem-solving technique that identifies the likely causes of a challenge and undertakes to fix it. It was named after Kaoru Ishikawa who first wrote about it in the 1960s. It also has a variation known as CEDAC or cause and effect diagram with the addition of cards. The tool is still used today by many different industries and has proved its worth on many different levels.
The diagram looks just like a fishs skeleton with the problem at its head and the causes for the problem feeding into the spine.
2001 Oldsmobile Alero V6 Engine Diagram When to Use A Fishbone Diagram. Each cause or reason for imperfection is a. A fishbone diagram is a tool that can help you perform a cause and effect analysis for a problem you are trying to solve. As the adage goes a picture is worth more than a thousand words. This type of analysis enables you to discover the root cause of a problem.
It was named after Kaoru Ishikawa who first wrote about it in the 1960s.
81 F150 Starter Wiring Diagram It also has a variation known as CEDAC or cause and effect diagram with the addition of cards. The tool is still used today by many different industries and has proved its worth on many different levels. A fishbone diagram is a tool that can help you perform a cause and effect analysis for a problem you are trying to solve. 5 ms and one p 6Ms in Six Sigma Practice Questions. It provides the visual representation of all the possible causes for a problem to analyze and find out the root cause. 6M6Ms is a mnemonic tool used primarily used when it comes to problem-solving or decision making.
Each cause or reason for imperfection is a.
Line Array Pa System Wiring Diagram A fishbone diagram is a tool that can help you perform a cause and effect analysis for a problem you are trying to solve. Advanced options are available to put the CE diagram to use for more complex problems. You could also use the 6M approach as a spine on each of a fish bone diagram and then ask the 5 whys to narrow down potential root cause. It provides the visual representation of all the possible causes for a problem to analyze and find out the root cause. The Cause and Effect diagram also known as Fishbone Diagram proves extremely beneficial when exploring or dissecting any production or industrial operations problems.
Fishbone diagram or Ishikawa diagram is a modern quality management tool that explains the cause and effect relationship for any quality issue that has arisen or that may arise.
2000 Dodge Durango Obd Wiring Diagram Example in Figure B below. Once all inputs are established on the fishbone you can proceed with the 5 Whys technique to drill down to the root causes. The fishbone diagram provides a visual representation of the various causes of a problem and serves as a good quality control tool providing project managers with a graphical representation of the cause and effect of a problem. 6M6Ms is a mnemonic tool used primarily used when it comes to problem-solving or decision making. Login to your account OR. The fishbone diagram is a very simple tool that permits effective and quick root causes in the pursuit of corrective actions.
It also has a variation known as CEDAC or cause and effect diagram with the addition of cards.
Wiring Diagrams For Volvo S60 6M6Ms is a mnemonic tool used primarily used when it comes to problem-solving or decision making. The head is the problem and the causes are connected with the spine. The 5 Whys can be also used as a part of the fishbone diagram visualization tool that helps to explore all causes of the problem. The 6 Ps is a mnemonic tool similar to the 6 Ms. This section requires you to be a Pass Your Six Sigma Exam member.
6M6Ms is a mnemonic tool used primarily used when it comes to problem-solving or decision making.
Nokia 3110 Circuit Diagram Download You could also use the 6M approach as a spine on each of a fish bone diagram and then ask the 5 whys to narrow down potential root cause. Each cause or reason for imperfection is a. Ishikawa pioneered a major quality movement while working at Kawasaki. Examples presented here will help you to understand the concept and you can also use the same template for your project. The fishbone diagram provides a visual representation of the various causes of a problem and serves as a good quality control tool providing project managers with a graphical representation of the cause and effect of a problem. Common uses of the Ishikawa diagram are product design and quality defect prevention to identify potential factors causing an overall effect.
The fishbone diagram is a very simple tool that permits effective and quick root causes in the pursuit of corrective actions.
Hopper Wiring Diagram It is difficult to find another tool with as many names. The fishbone diagram also called the Ishikawa diagram is one other instrument to give you a visible illustration of your 5-why evaluation. This tool can be created electronically but it can also easily be done on a whiteboard or a piece of paper. It is one primarily used by manufacturing industries. Both are used to categorize causes on an Ishikawa cause effect diagram.
The fishbone diagram also called the Ishikawa diagram is one other instrument to give you a visible illustration of your 5-why evaluation.
Wiring Diagram Ford Focus 2009 Portugues The fishbone diagram provides a visual representation of the various causes of a problem and serves as a good quality control tool providing project managers with a graphical representation of the cause and effect of a problem. This tool is also called a cause and effect diagram or an Ishikawa diagramThese names can be used interchangeably. Cause and effect is a systematic approach to explore various causes leading to a problem condition It is a group activity in which all the stakeholders. The diagram looks just like a fishs skeleton with the problem at its head and the causes for the problem feeding into the spine. Ishikawa diagrams also called fishbone diagrams herringbone diagrams cause-and-effect diagrams or Fishikawa are causal diagrams created by Kaoru Ishikawa that show the potential causes of a specific event. It also has a variation known as CEDAC or cause and effect diagram with the addition of cards.
The fishbone diagram or Ishikawa diagram is a cause-and-effect diagram that helps managers to track down the reasons for imperfections variations defects or failures.
Chevy Equinox 2007 Pnp Wiring Diagram Fishbone is also known as cause and effect diagram or Ishikawa diagram. This tool is also called a cause and effect diagram or an Ishikawa diagramThese names can be used interchangeably. Once all inputs are established on the fishbone you can proceed with the 5 Whys technique to drill down to the root causes. This diagram looks like a fish skeleton. The fishbone diagram is a very simple tool that permits effective and quick root causes in the pursuit of corrective actions.
5 ms and one p 6Ms in Six Sigma Practice Questions.
1997 Honda Accord Wiring Diagrams Automotive Log in or Sign up in seconds with the buttons below. The fishbone diagram also called the Ishikawa diagram is one other instrument to give you a visible illustration of your 5-why evaluation. It also has a variation known as CEDAC or cause and effect diagram with the addition of cards. The diagram looks just like a fishs skeleton with the problem at its head and the causes for the problem feeding into the spine. Login to your account OR. This type of analysis enables you to discover the root cause of a problem.
Therefore many experts call it a fishbone.
Wiring Diagram For Alternating Relay Half three of a sequence on the five-whys. It is difficult to find another tool with as many names. It provides the visual representation of all the possible causes for a problem to analyze and find out the root cause. It is one primarily used by manufacturing industries. The 6 Ms were traditionally used for fishbone diagrams on the shop floor or other production environments.
Examples presented here will help you to understand the concept and you can also use the same template for your project.
67 Camaro Wiring Diagram It is also called as Ishikawa diagram and cause and effect diagram. The 5 Whys can be also used as a part of the fishbone diagram visualization tool that helps to explore all causes of the problem. The Cause and Effect diagram also known as Fishbone Diagram proves extremely beneficial when exploring or dissecting any production or industrial operations problems. The fishbone diagram provides a visual representation of the various causes of a problem and serves as a good quality control tool providing project managers with a graphical representation of the cause and effect of a problem. This type of analysis enables you to discover the root cause of a problem. 6M6Ms is a mnemonic tool used primarily used when it comes to problem-solving or decision making.
A fishbone diagram is a tool that can help you perform a cause and effect analysis for a problem you are trying to solve.
Wiring Diagram For Trailer Lights 6 Plug This section requires you to be a Pass Your Six Sigma Exam member. It provides the visual representation of all the possible causes for a problem to analyze and find out the root cause. When to Use A Fishbone Diagram. The fishbone or Ishikawa diagram is one other technique to visualize 5-why evaluation and permits you to classify your evaluation into broad classes. The tool is still used today by many different industries and has proved its worth on many different levels.
Half three of a sequence on the five-whys.
Plymouth Voyager Fuse Box Diagram This diagram looks like a fish skeleton. The 6 Ms were traditionally used for fishbone diagrams on the shop floor or other production environments. It is a problem-solving technique that identifies the likely causes of a challenge and undertakes to fix it. This tool can be created electronically but it can also easily be done on a whiteboard or a piece of paper. Login to your account OR. It was named after Kaoru Ishikawa who first wrote about it in the 1960s.
This section requires you to be a Pass Your Six Sigma Exam member.
Stereo Wiring Diagram 2002 Chevy Avalanche Log in or Sign up in seconds with the buttons below. It is a simple tool that is used for brainstorming issues and reasons of particular problems. The ishikawa diagram was founded in 1968 by Kaoru Ishikawa. The fishbone diagram or Ishikawa diagram is a cause-and-effect diagram that helps managers to track down the reasons for imperfections variations defects or failures. One of the fundamental tools he used on many of his projects was the ishikawa diagram.
Situs ini adalah komunitas terbuka bagi pengguna untuk membagikan apa yang mereka cari di internet, semua konten atau gambar di situs web ini hanya untuk penggunaan pribadi, sangat dilarang untuk menggunakan artikel ini untuk tujuan komersial, jika Anda adalah penulisnya dan menemukan gambar ini dibagikan tanpa izin Anda, silakan ajukan laporan DMCA kepada Kami.
Jika Anda menemukan situs ini bagus, tolong dukung kami dengan membagikan postingan ini ke akun media sosial seperti Facebook, Instagram dan sebagainya atau bisa juga bookmark halaman blog ini dengan judul 6m Fishbone Diagram Projects dengan menggunakan Ctrl + D untuk perangkat laptop dengan sistem operasi Windows atau Command + D untuk laptop dengan sistem operasi Apple. Jika Anda menggunakan smartphone, Anda juga dapat menggunakan menu laci dari browser yang Anda gunakan. Baik itu sistem operasi Windows, Mac, iOS, atau Android, Anda tetap dapat menandai situs web ini.